fhalcon® truck makes it possible for you to manage completely all weighbridge processes. It can be done either manually by your staff or by means of driver self-service with language selection, transponder card dispenser, image archiving, automatic number plate recognition and signature pad.
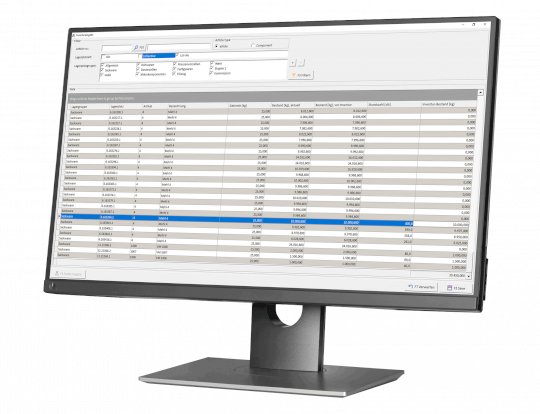
basics
The foundation and starting point for all fhalcon® modules is always the master data. The most important data for fhalcon® truck includes:
Personal master data:
- Three-stage address management up to the silo / farm
- Supplier / Delivery person
- Carrier
Vehicle master data:
- Vehicle types
- Registration number
- Weights
Product master data:
- Components and item master data
- Item-related raw material qualities
- Item declarations
- Density
- Material flow balance values
Storage and storage space / cell master data:
- Technical dimensions, capacity and volumes
- Minimum stock level
- Approval for filling / emptying
- Approval for the automatic system
- Mixing area for goods tracking and tracing
Transponder master data:
- Card type (day or permanent)
- Validity
- Vehicle allocation
- Person allocation
- Language
User management:
- Module-related
- Can be maintained by the customer
- Logging
- Evaluation
The consistent recording of all product flows starts with the incoming goods. With our weighing module, you can integrate calibratable scales evaluation devices into your overall system.
- Can be connected to all standard scales evaluation devices
- TCP / IP protocol or comparable
- Works with multiple scales
- Weighing can be done at any workstation in the network
- Incoming / Outgoing goods
- External weighing
- Gross weighing
- Check weighing
- Loose trips (fhalcon® export module)
- Bagged trips (fhalcon® export module)
- Bagged goods purchases and sales
- Resetting via dialogue
- Saving or printing of alibi data
- Printing or direct emailing (mailing option) of receipts with signature (digital signature option) for each process
- Flexible layouts according to customer specifications
- Integration of logos or letterheads
- Person or product-related layouts / printer
- Printing of delivery notes with declaration
- Printing of identification labels for retained samples
- Permanent display of the weight of the approved scales
- Allocation of blank weighings
The stock management allows you to maintain an overview of where products are located and stock levels. This guarantees a smooth production process and forms the basis for effective goods tracking and tracing.
- Stock bookings can be made immediately after the weight has been determined
- Direct or process-controlled cell booking (fhalcon® import or fhalcon® export)
- Product-related
- Storage space-related (e.g. cell, area or space)
- Group-related (can be defined and configured freely)
- Storage location and space-related (e.g. hangars)
- Lot-related (bagged goods / piece goods)
- Component and cell inventories
- Storage space-related
- Group-related
- Storage location or storage space-related
- Lot-related
- Movement lists (each booking with reference)
- Visual inspection and logging of cell cleaning with user and flexible warning text
- Graphic inventory
- Minimum stock lists
Regulatory requirements are becoming increasingly comprehensive and complicated to fill out manually or on paper. Our goods tracking and tracing module supports you at the push of a button. The search works both forwards and backwards, and from one process to another.
- Process-related in all directions
- Lot-related and FiFo (First in First out)
- Consistent monitoring of stock movements
- Adjustable mixing range to take the mixing behaviour / funnel formation of a silo into consideration
- Address data output for purchases and sales
- Animal feed sales list directly as Excel file incl. all data required by the relevant authorities
- Address data (supplier / invoice recipient or dealer / delivery address)
- Delivery date
- Quantity delivered
- Type of feed
- Composition / Structure
- Commercial name
- Item number
- Process number
- ID number of the lot (all batches involved)
- Delivery note number
- Target animal
- Maximum usage rate in accordance with the directions for use in %
- Mixed quantity of the component concerned in kg
- Mixed proportion of the component concerned in %
- Mixed proportion, according to the formula, of the component concerned in %
- Follow-up delivery received on
- Direct access to documents stored in the long-term archive
- Display of whether the process that you are looking for has been used or is still in stock
- Direct search for orders / lots
Checking your inventory regularly helps to ensure that your stock management is up to date and guarantees the traceability of goods. It also helps you to detect any irregularities and possible product loss.
- Freezing of stock for recalculation later once the inventory has been completed
- Storage space-related (e.g. cell, area or space)
- Lot-related (bagged goods / piece goods)
- Printing of count lists
- Export of count lists
- Storage space group-related count lists
- Checking of issued and returned lists
- Input of free meters for silos for automatic stock calculation based on the cell dimensions and product bulk density
- Quick entry as a list
- Multiple inputs with comparison
- Checklists for finished products and raw materials with comparison of purchases, the produced quantity and sales, incl. a visualisation of the differences
- Comparison of inventories
- Scanner-supported inventory
All processes are logged and archived. Our statistics module allows you to review and evaluate all processes and movements.
Evaluation options:
- Incoming weight notes
- Outgoing weight notes
- External weight notes
- Control weight notes
- Stored quantities
- Removed quantities
- Stock movements
- Storage space movements
- Product movements
- Process movements
Statistics functions:
- Flexibly configurable
- Filter, group and sort within lists
- Display or hide columns
- Adjust the width and order of the columns
- Totals and subtotals
- User and workstation-related, freely configurable list layouts
- Direct export to Excel or other formats
- Reprint receipts
Document archiving system for your paperless office. Printed receipts and important logs are automatically saved in the file system.
- The printed receipts are automatically saved as PDF files
- All process data is automatically saved as XML files
- Several storage locations are used
- Data is saved in a clear, chronological folder structure
- Re-printing is done from the archive
- Automatic archiving after modifications have been made to receipts
- Image archiving (camera integration option)
- Archiving of external documents (digitalize shipping documents option)
- Automatic sending of receipts (mailing option)
- Archiving with digital signature (digital signature option)
- Provision of archive data for third-party systems
options
How order management works today: You can prevent incorrect information and inputs either via an interface (interface options) or by recording in our system.
- Inputting and management of orders
- Incoming loose / bagged goods
- Purchase contracts
- Outgoing loose / bagged goods
- Sales contracts
- Quick entry of outgoing loose goods
- Recommendations for farm / silo from previous deliveries
- Automatic, manual or scanner-supported recording of actual purchasing and / or sales quantities (scan option)
- Order or process-related weighing
- Weighed orders disappear from the pool
- Order tracking
- Filter and evaluate by person or product
- Contract booking
Transponder card-controlled driver self-service which allows the truck driver to start and manage processes.
- Self-weighing via transponder cards
- Incoming goods
- Outgoing goods
- External weighing
- Check weighing
- Follow-up weighing
- Blank weighing
- Automatic printing with signature (digital signature option) after second weighing
- Receipt and label printing
- Automatic booking
- Supports a wide range of different types of transponder cards and readers
- Contactless
- Entry card reader
- Card dispenser
- Desktop device
- TCP / IP protocol or comparable
- Check to see whether a valid process exists
- Information display for readers with display screens
- Opening of gates and doors (gate management option)
- Control of traffic lights and lights
- Holding of transponder cards, as long as the process is running (entry card reader and card dispenser)
- Allocation of day and permanent cards
The automated registration / identification of vehicles by their number plate makes the recording and identification process easier.
- Reading out and saving of the read registration number
- Validity check
- Supports a wide variety of different camera types
- Check to see whether the vehicle exists and has been approved
- Check to see whether a valid process exists
- Automatic weighing
- Opening of gates and doors (gate management option)
- Suggestion of the read registration number with registration or further processing
Access control and opening of gates and doors for admission to site, hoppers, loading lanes or driver’s cabs.
- Triggered via transponder cards (transponder self-service option)
- Triggered via automatic number plate identification (number plate identification option)
- Validity check
- Check to see whether a valid process exists, only approved if the process exists or has been allocated
Action-controlled, process-related display and archiving of camera images.
- Archiving of camera images
- Allows for an unattended or driver self-weighing
- Supports a wide variety of different network cameras
- Process-related storage and display for the following processes
- Weighing with truck scales (fhalcon® truck)
- Truck loading (fhalcon® export)
- Receiving hopper (fhalcon® import)
- Driver’s cab for handheld device allocation / handover (fhalcon® export)
- Tank loading (fhalcon® export)
- Sampling (fhalcon® analysis)
- Integration into long-term archives
- Displays camera images in the software (fhalcon® analysis, fhalcon® import, fhalcon® export and fhalcon® visualization)
Digital signature for receipts and documents. Print and archive with a signature.
- Connection of signature pads
- Display of the documents that require signature
- Automatic scroll function if documents exceed the screen size
- Validity check
- Printing of signed receipts
- Archiving of signed receipts
Digitisation of accompanying documents.
- Integration of document scanner or office printer with scan function
- Automatic allocation thanks to clear file names or via the selection screen with preview
- Attachment of scanned documents to the archived receipt
Driver registration and self-weighing software.
- Available languages displayed as flags
- Selection and saving of the language
- Input of the registration number or automatic determination via number plate identification (number plate identification option)
- Connection of motorised transponder card readers and dispensers
- Issue / Entry of transponder cards
- Connection of signature pad (digital signature option)
- Selection of delivery person / collector or third party
- Selection of the vehicle combination
- Delivery person
- Input of previous loads
- Collector
- Input of previous loads
- Input of previous trips
- Detailed planning with tank division
- Tank weight check
- Overall weight check
Automatic emailing of receipts, documents and statistics.
- Automatic emailing of incoming goods receipts to the supplier and / or delivery person after second weighing
- Automatic emailing of outgoing goods receipts to the customer and / or end customer after the loading process has been completed
- Can choose whether documents are sent or printed by e-mail and paper, only e-mail or only paper in the master data
- Integration into the on-site system structure
- Integration into the on-site email system
- Sending of emails from the programmes
- Automated, time-controlled sending of emails with attachments
Seamless integration into your ERP system or other third-party system.
- Import of master data such as
- People
- Products
- Declarations
- Vehicles
- Transponder cards
- Import and export of orders
- Export of all receipts
- Export of all movement data
- Standardised and / or customer-specific
- Different forms of communication to third-party systems are supported
- Online, e.g. through sockets, web services or JSON
- File-based, e.g. via ASCII, CSV, XML or IDoc
- Direct exchange via interfaces-databases, for example
- All data exchanged via interfaces can also be entered or maintained manually by dialogues
- Export of the data from the archive system with customisable file names (archive option)
screens
Contact
Give us a call!
Do you have a question about any of our services? Would you like to discover the options offered by the fhalcon® Software Suite live? Simply contact our specialists. We would be happy to take the time to talk to you.